inlet guide vanes
Summary
Discover the essential role of inlet guide vanes in optimizing turbine performance. Learn about their design, function, and applications in our comprehensive guide.
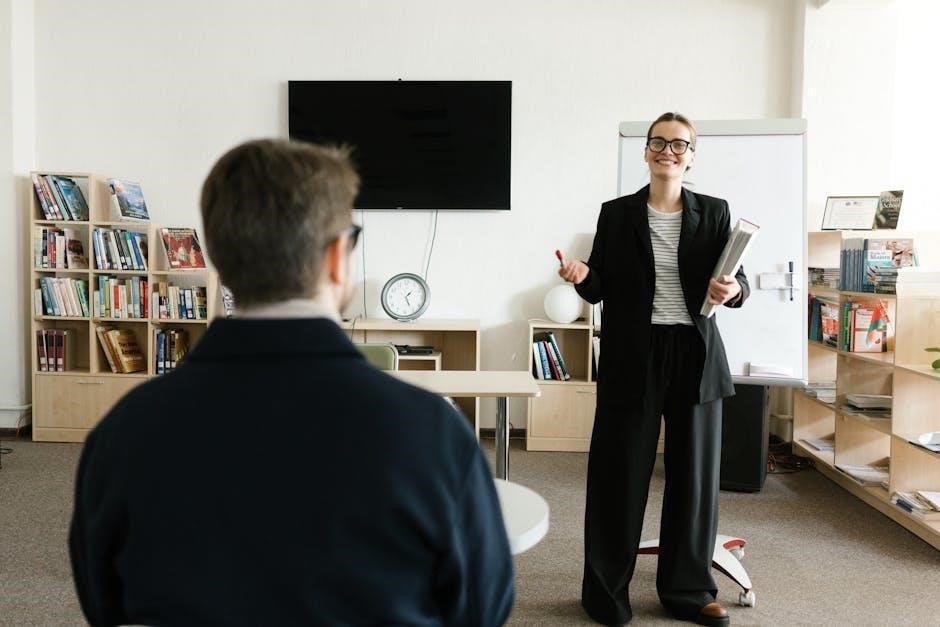
Inlet guide vanes (IGVs) are critical components in compressors‚ regulating airflow and enhancing performance. They are designed to optimize efficiency and pressure recovery‚ playing a vital role in various applications.
- They direct incoming air to the compressor blades.
- IGVs help reduce energy consumption and improve stability.
- Their design has evolved over time to meet modern demands.
1.1 Definition and Basic Function
Inlet guide vanes (IGVs) are stationary components located at the inlet of compressors. Their primary function is to direct incoming air at optimal angles and velocities‚ ensuring smooth flow into the compressor blades. By regulating airflow and pressure distribution‚ IGVs enhance compressor performance‚ efficiency‚ and stability across various operating conditions.
- They are designed to minimize turbulence and maximize airflow uniformity.
- IGVs play a crucial role in improving compressor surge margins and overall system reliability.
1.2 Historical Development and Evolution
Inlet guide vanes (IGVs) have evolved significantly since their introduction in early turbo machinery. Initially simple fixed vanes‚ they were later optimized for improved airflow control. The 20th century saw advancements in materials and designs‚ enabling variable-angle IGVs for enhanced performance. Modern IGVs integrate smart technologies‚ offering real-time adjustments for optimal compressor operation.
- Early IGVs were fixed and less efficient.
- Advancements in aerodynamics and materials improved their design.
- Variable IGVs emerged in the 1980s‚ revolutionizing compressor control.
Role of Inlet Guide Vanes in Compressor Performance
Inlet guide vanes play a pivotal role in enhancing compressor performance by regulating airflow and optimizing pressure recovery. They ensure efficient operation across varying conditions‚ improving overall system stability and output.
- They stabilize airflow at compressor inlet.
- IGVs minimize energy losses and enhance efficiency.
- Optimal vane alignment reduces mechanical stress.
2.1 Airflow Control and Regulation
Inlet guide vanes regulate airflow by directing air at optimal angles to compressor blades‚ ensuring efficient operation. They maintain uniform velocity distribution‚ reducing turbulence and enhancing stability. This precise control minimizes energy losses and prevents stall or surge conditions‚ critical for consistent compressor performance across varying operating conditions.
- Optimizes air angle for smoother entry.
- Reduces turbulence for better efficiency.
- Prevents stall and surge events.
2.2 Pressure Recovery and Efficiency Optimization
Inlet guide vanes enhance pressure recovery by minimizing losses during airflow direction changes. Their optimized design ensures efficient energy transfer‚ reducing turbulence and maximizing compressor performance. By maintaining uniform flow distribution‚ they contribute to higher overall efficiency‚ making them essential for modern compressor systems aiming to reduce energy consumption and improve operational reliability.
- Minimizes energy losses during airflow redirection.
- Enhances pressure recovery for better efficiency.
- Reduces turbulence for smoother operation.
Design Considerations for Inlet Guide Vanes
Inlet guide vanes are designed to optimize airflow and efficiency‚ with careful attention to geometrical shape and material selection for durability and performance.
- Geometrical configuration ensures smooth airflow.
- Shape design maximizes efficiency and pressure recovery.
- Materials are chosen for strength and longevity.
3.1 Geometrical Configuration and Shape
The geometrical configuration and shape of inlet guide vanes are critical for optimizing airflow direction and aerodynamic efficiency. The design ensures minimal energy loss while maximizing pressure recovery. Key features include precisely angled surfaces‚ smooth curvature‚ and strategic placement to align with compressor blades.
- Optimized angles reduce flow disturbances.
- Curved surfaces enhance flow uniformity.
- Precision placement minimizes mechanical stress.
3.2 Material Selection for Durability
Material selection for inlet guide vanes is crucial for ensuring durability under harsh operating conditions. High-strength‚ corrosion-resistant alloys like titanium and nickel-based superalloys are commonly used. These materials withstand extreme temperatures‚ mechanical stress‚ and erosion‚ ensuring longevity and optimal performance.
- Titanium alloys offer lightweight strength and corrosion resistance.
- Nickel-based superalloys provide exceptional heat tolerance.
- Advanced manufacturing techniques enhance material integrity.
Applications of Inlet Guide Vanes
Inlet guide vanes are widely used in gas turbines‚ turbochargers‚ and industrial compressors to regulate airflow and enhance performance. They are also integrated into aircraft engines for optimal efficiency.
- Gas turbines benefit from improved pressure recovery.
- Turbochargers rely on IGVs for airflow control.
- Industrial compressors utilize them for efficiency optimization.
- Aircraft engines integrate IGVs for enhanced performance.
4.1 Use in Gas Turbines
In gas turbines‚ inlet guide vanes (IGVs) are essential for directing airflow and optimizing efficiency. They regulate inlet air angles‚ reducing energy losses and enhancing stability during operation. IGVs improve pressure recovery‚ ensuring smooth airflow into the compressor. Their design plays a critical role in minimizing emissions and maximizing turbine performance‚ making them indispensable in modern gas turbine systems for power generation and industrial applications.
- Enhance airflow regulation and efficiency.
- Reduce energy losses and emissions.
- Optimize compressor inlet conditions.
4.2 Implementation in Turbochargers
In turbochargers‚ inlet guide vanes (IGVs) enhance performance by optimizing airflow to the compressor. They improve boost pressure and reduce turbo lag‚ ensuring smoother acceleration. IGVs adjust to varying engine speeds‚ maximizing efficiency and power output. Their implementation boosts fuel efficiency and reduces emissions‚ making them a crucial component in modern turbocharged engines for automotive and industrial applications.
- Optimize compressor inlet airflow for better performance.
- Reduce turbo lag and improve engine responsiveness.
- Enhance fuel efficiency and minimize emissions.
4.3 Role in Industrial Compressors
Inlet guide vanes (IGVs) play a pivotal role in industrial compressors by regulating airflow and pressure. They enhance compressor efficiency‚ reduce energy consumption‚ and minimize operational noise. IGVs are essential for maintaining stable operation across varying load conditions‚ ensuring optimal performance in large-scale industrial applications such as power generation and manufacturing processes.
- Regulate airflow for consistent compressor performance.
- Reduce energy consumption and operational costs.
- Minimize noise and vibrations during operation.
4.4 Integration into Aircraft Engines
In aircraft engines‚ inlet guide vanes (IGVs) are crucial for managing airflow at high altitudes. They enhance compressor performance‚ ensuring efficient air pressure recovery and stable engine operation. IGVs are designed to withstand extreme conditions‚ contributing to fuel efficiency and reducing emissions in aerospace applications.
- Optimize airflow in high-altitude conditions.
- Ensure stable engine operation and fuel efficiency.
- Contribute to reduced emissions and noise.
Variable Inlet Guide Vanes
Variable inlet guide vanes (VIGVs) are adjustable components that optimize compressor performance by dynamically controlling airflow. Their ability to adapt to changing conditions enhances efficiency and operational flexibility.
- Adjust to varying engine requirements.
- Improve compressor stability and performance.
- Enable real-time optimization of airflow.
5.1 Concept and Operational Principles
Variable inlet guide vanes (VIGVs) are adjustable aerodynamic components that dynamically control airflow entering a compressor. By rotating to optimize angle and incidence‚ they ensure efficient airflow regulation. This adaptability enables real-time adjustments‚ enhancing compressor performance and stability across varying operational conditions‚ making them crucial in modern gas turbines and engines for improved efficiency and responsiveness.
- Adjustable design for dynamic airflow control.
- Optimize compressor performance and stability;
- Enable real-time operational adjustments.
5.2 Advantages Over Fixed Vanes
Variable inlet guide vanes (VIGVs) offer superior adaptability compared to fixed vanes‚ enabling dynamic adjustments to airflow conditions. This flexibility enhances compressor efficiency‚ reduces energy losses‚ and minimizes emissions. VIGVs also improve surge margin and operational stability‚ making them ideal for diverse applications requiring precise airflow control and optimal performance across varying conditions.
- Improved efficiency and reduced energy losses.
- Enhanced operational stability and surge margin.
- Minimized emissions and environmental impact.
- Better adaptability for varying applications.
Dynamic Response and Control
Dynamic response and control systems enable real-time adjustments of inlet guide vanes‚ optimizing compressor performance under varying conditions. Advanced sensors and actuators ensure precise airflow regulation and stability.
- Real-time adjustments for optimal performance.
- Advanced sensors and actuators for precise control.
- Enhanced stability during variable operating conditions.
6.1 Real-Time Adjustments for Performance
Real-time adjustments of inlet guide vanes enable dynamic control over airflow‚ optimizing compressor performance. Sensors monitor operating conditions‚ while actuators execute precise vane movements. This ensures optimal efficiency‚ stability‚ and responsiveness during varying load conditions‚ enhancing overall system reliability and adaptability.
- Sensors continuously monitor pressure‚ temperature‚ and flow rates.
- Actuators adjust vane angles based on real-time data.
- Dynamic precision ensures stable operation across diverse conditions.
6.2 Active Control Systems for Optimal Flow
Active control systems integrate advanced sensors and automation to optimize inlet guide vane performance. These systems leverage real-time data to adjust vane angles‚ ensuring precise airflow control. By incorporating feedback loops and predictive algorithms‚ they maintain optimal flow characteristics‚ reducing energy losses and enhancing overall system efficiency.
- Sensors provide real-time flow and pressure data.
- Automated systems adjust vanes for optimal performance.
- Predictive algorithms anticipate and adapt to changing conditions.
Installation and Maintenance Tips
Proper installation and regular maintenance are crucial for optimal IGV performance. Ensure alignment during installation and clean vanes periodically to prevent debris buildup. Inspect for wear regularly.
- Align vanes precisely during installation.
- Clean vanes to avoid debris accumulation.
- Inspect for wear and tear.
7.1 Best Practices for Installation
Ensure proper alignment of IGVs with airflow direction for optimal performance. Use torque wrench for secure mounting without overtightening. Calibrate vanes post-installation for precise control. Inspect for obstructions in the inlet to maintain smooth airflow. Apply appropriate sealing to prevent leakage. Conduct post-installation testing to verify efficiency and functionality. Follow manufacturer guidelines for precise installation steps.
- Align IGVs with airflow direction.
- Use a torque wrench for secure mounting.
- Calibrate vanes post-installation.
- Inspect for inlet obstructions.
- Apply proper sealing techniques.
- Conduct post-installation testing.
7.2 Regular Maintenance for Longevity
Inspect IGVs for debris and erosion monthly. Clean vanes with compressed air or mild detergents to prevent corrosion; Lubricate pivot points every 500 operating hours. Check for alignment shifts due to vibration. Replace worn seals to maintain efficiency. Schedule annual performance checks to ensure optimal airflow and pressure recovery.
- Inspect monthly for debris and wear.
- Clean with compressed air or mild detergents.
- Lubricate pivot points every 500 hours.
- Check alignment and replace worn seals.
- Perform annual performance evaluations.
Future Trends and Innovations
Smart inlet guide vanes with real-time adjustments are emerging‚ enhancing efficiency and adaptability. Advanced materials and AI-driven systems promise improved performance and sustainability in compressors and turbines.
- Integration of AI for dynamic control.
- Development of self-adjusting vane systems.
- Use of lightweight‚ high-strength materials.
8.1 Development of Smart Inlet Guide Vanes
Smart inlet guide vanes integrate sensors and real-time data analysis to optimize compressor performance dynamically‚ ensuring peak efficiency across varying operational conditions and significantly reducing emissions.
- Advanced algorithms predict optimal vane angles for different load scenarios‚ enhancing performance adaptability.
- Integration with AI-driven systems enables proactive maintenance‚ extending equipment lifespan and operational reliability.
8.2 Integration with Advanced Materials
The use of advanced materials in inlet guide vanes enhances durability and performance under extreme conditions. Lightweight composites and high-strength alloys are now being utilized to improve efficiency and reduce weight‚ making them ideal for aerospace and industrial applications.
- 3D-printed materials enable complex geometries for optimized airflow.
Case Studies and Real-World Examples
Real-world applications of inlet guide vanes demonstrate their effectiveness in enhancing compressor performance across industries. Case studies highlight improved efficiency in aerospace and energy sectors through optimized airflow control.
- Successful implementations in industrial compressors.
9.1 Successful Implementation in Industrial Settings
Inlet guide vanes have proven instrumental in industrial compressors‚ enhancing performance and efficiency. Their application in power generation and manufacturing sectors has reduced energy consumption and increased operational stability. Real-world examples demonstrate significant improvements in airflow regulation‚ leading to higher productivity and cost savings. Industries benefit from customized IGV designs tailored to specific operational demands‚ ensuring optimal results.
- Improved airflow control in industrial compressors.
- Enhanced efficiency in power generation plants.
9.2 Applications in Aerospace Engineering
In aerospace engineering‚ inlet guide vanes are pivotal for aircraft engine performance. They optimize airflow into compressors‚ ensuring efficient thrust generation at varying altitudes; Their implementation enhances fuel efficiency and reduces emissions‚ critical for modern aviation. Customized designs for aircraft engines highlight their adaptability and importance in maintaining operational excellence and safety in the aerospace sector.
Environmental Impact and Sustainability
Inlet guide vanes contribute to environmental sustainability by enhancing compressor efficiency‚ reducing energy consumption‚ and lowering emissions. Their optimized design supports greener operations‚ aligning with global sustainability goals.
- Improved efficiency reduces fuel consumption.
- Lower emissions promote cleaner energy use.
10.1 Energy Efficiency Contributions
Inlet guide vanes enhance energy efficiency by optimizing airflow and pressure recovery in compressors. Their design ensures minimal energy loss‚ contributing to reduced power consumption and higher overall system performance. This optimization leads to significant energy savings‚ making them a key component in sustainable and efficient compressor systems.
- Optimizing airflow and pressure recovery.
- Reducing energy loss and power consumption.
- Enhancing overall system efficiency and sustainability.
10.2 Reduction of Emissions
Inlet guide vanes contribute to emission reduction by improving compressor efficiency‚ lowering fuel consumption‚ and reducing operational waste. Enhanced airflow management decreases energy requirements‚ resulting in lower greenhouse gas emissions and supporting environmental sustainability goals.
- Lowering fuel consumption and operational waste.
- Reducing greenhouse gas emissions.
- Supporting environmental sustainability goals.
Challenges and Limitations
Inlet guide vanes face challenges like mechanical complexity and operational constraints. Their design requires precision to avoid flow disruptions and material degradation‚ impacting performance and longevity.
- Mechanical complexity in variable vane systems.
- Operational constraints affecting flow stability.
- Material degradation over time.
11.1 Technical Challenges in Design
Inlet guide vanes face technical challenges in design‚ including balancing aerodynamic performance and mechanical integrity. Complex geometries‚ material limitations‚ and manufacturing tolerances must be addressed to ensure optimal airflow and durability. Additionally‚ variable vane systems require precise actuation mechanisms‚ adding layers of complexity to their engineering and operation.
- Complex geometries for aerodynamic efficiency.
- Material limitations under extreme conditions.
- Manufacturing tolerances for precision.
11.2 Operational Limitations and Constraints
Inlet guide vanes face operational limitations‚ including susceptibility to fouling‚ wear‚ and erosion‚ which reduce efficiency over time. Environmental factors like temperature and humidity can impair performance. Additionally‚ mechanical stress from frequent adjustments and system vibrations pose challenges. These constraints necessitate robust designs and regular maintenance to ensure optimal functionality across varying operating conditions.
- Susceptibility to fouling and wear.
- Environmental impacts on performance.
- Mechanical stress from system vibrations.
Inlet guide vanes play a pivotal role in compressor efficiency and performance. Future advancements promise smarter designs‚ integrating advanced materials and technologies to enhance functionality and sustainability further.
- Optimized designs for better efficiency.
- Integration of advanced materials.
- Enhanced sustainability in future models.
12.2 Potential for Future Advancements
12.1 Summary of Key Points
Inlet guide vanes (IGVs) are essential for optimizing compressor performance by regulating airflow and enhancing efficiency. Their design has evolved to address technical challenges‚ with applications spanning gas turbines‚ turbochargers‚ and aerospace. Material selection and geometrical precision are critical for durability and functionality. Future trends include smart IGVs and advanced materials‚ promising improved sustainability and performance across industries.
- IGVs optimize airflow and efficiency.
- Design advancements address technical challenges.
- Applications span multiple industrial sectors.